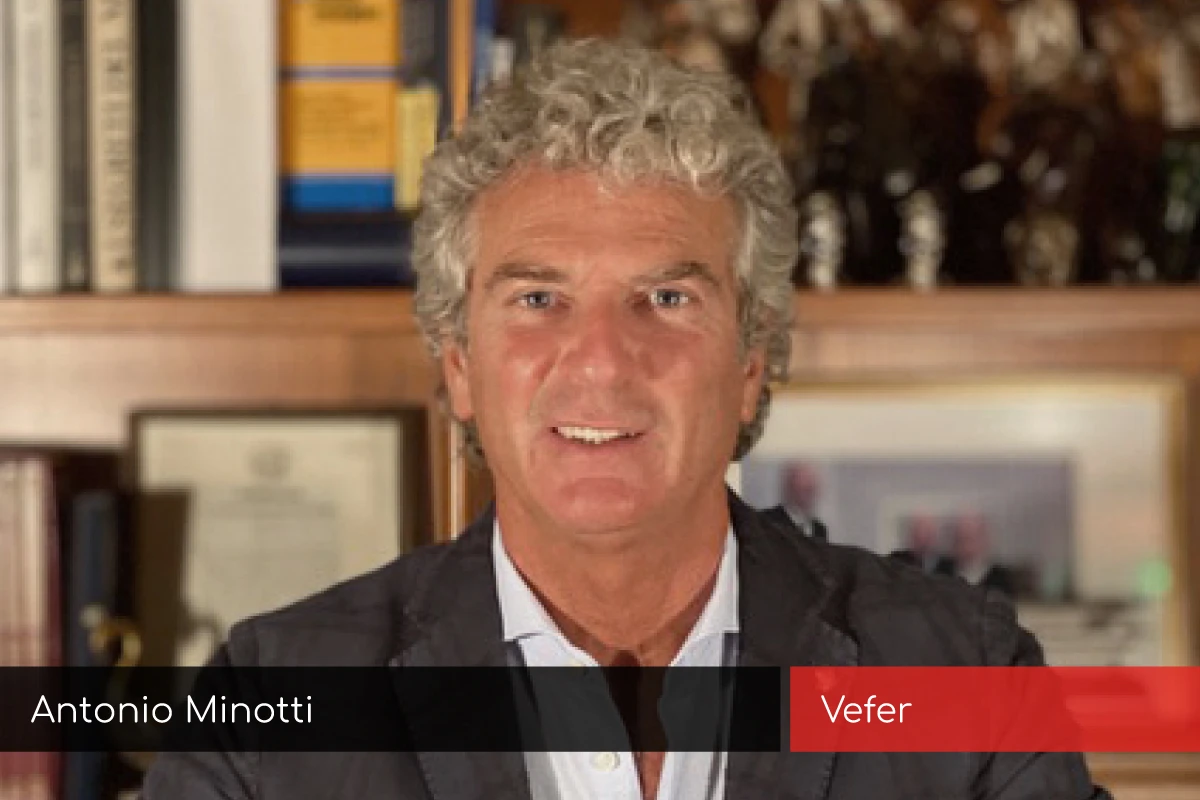
La recherche, le respect et l'innovation sont le leitmotiv de Vefer, une réalité entrepreneuriale à l'avant-garde en Italie et en Europe dans la production de polyuréthanes flexibles pour le blocage.
Toujours attentive aux multiples exigences du marché, l'entreprise lissoise poursuit sa politique de recherche et d'innovation visant à produire des polyuréthanes de plus en plus performants, confortables et durables.
C'est justement de produits durables, d'économie circulaire, de réduction de la consommation de matières premières et de durabilité que nous avons parlé avec Antonio Minotti, directeur général de Vefer.
La durabilité est aujourd'hui considérée comme une grande opportunité pour les entreprises. Comment cette préoccupation pour l'environnement s'exprime-t-elle dans votre entreprise ?
Vefer a toujours été sensible au thème de la durabilité et, aujourd'hui encore plus, nous sommes en première ligne pour apporter notre contribution.
La production est gérée de manière à minimiser l'utilisation des ressources naturelles, à réduire la pollution et les impacts négatifs sur l'environnement et à garantir des conditions de travail équitables pour les employés.
Vefer, qui a toujours été un pionnier en matière de protection de l'environnement, a été le premier fabricant de mousse de polyuréthane en Europe à produire des mousses avec des matières premières provenant de sources renouvelables, des polyols dérivés de l'acide ricinoléique. C'est ainsi qu'est née la catégorie de mousses Biogreen®.

Biogreen® est un produit fabriqué à partir de matières premières renouvelables, naturelles et non contaminantes.
La production de toutes les agrafes de l'entreprise est réalisée en utilisant les déchets de production issus de la transformation de la mousse, c'est-à-dire la deuxième matière première, et aucune mousse vierge n'est utilisée. En outre, tous les déchets de production de l'entreprise qui ne sont pas utilisés pour la fourniture d'agrafes d'ameublement sont vendus en paquets pressés pour être réutilisés dans le domaine des tapis et des charges dans les asphaltes insonorisants.
Récemment, Vefer a mis en place une collaboration avec Repsol, l'un des principaux producteurs de polyols, la matière première pour la production de polyuréthane, afin de développer des mousses produites à partir de polyols dérivés du recyclage de matelas en mousse de polyuréthane post-consommation, ce qui a donné naissance à la classe de polyuréthanes CIRCULARREFOAM®.
Cette production, en coopération avec l'important organisme de certification OETI de Vienne, a permis d'obtenir le premier certificat de qualité pour les mousses produites en mode circulaire.

Mousse de polyuréthane écologique CIRCULARREFOAM® fabriquée à partir de 15 % de polyols recyclés
Vefer a-t-il des projets en matière d'efficacité et de réduction de la consommation de matières premières ?
Vefer a formulé dans son plan industriel son intention d'adopter le modèle de production connu sous le nom de Lean Plastic, dérivé du système Toyota appliqué spécifiquement au monde du plastique.
Le plan prévoyait l'identification d'une entreprise pour soutenir ce projet dans une phase initiale de vérification afin de mettre en évidence les domaines d'amélioration et, par la suite, de mettre en œuvre les activités nécessaires pour appliquer ce qui a été appelé le "système de production Vefer".
Le plan industriel prévoit une amélioration de l'efficacité des Lay-Outs des départements dans une perspective Lean, une réduction des déchets et une amélioration de l'intralogistique, garantissant le flux de valeur tout au long de l'axe de l'entreprise.
Une autre question concerne les matières premières, puisqu'elles sont liées à des formulations précises pour obtenir des mousses aux propriétés techniques prédéfinies.
Pour réduire la consommation de matières premières, Vefer a adopté un plan industriel qui comprend une approche diversifiée : l'utilisation de polyols dérivés de matelas post-consommation (mousses CIRCULARREFOAM®), un projet en cours avec une coopération européenne, et la réduction des lots spéciaux internes (produits de second choix).
La réduction des produits de second choix a une double efficacité : d'une part, une réduction de la consommation de matières premières et, d'autre part, des économies d'énergie pour éviter le retraitement et la poursuite du transport interne, avec pour conséquence une augmentation des déchets de mise en forme.